In today’s fast-paced world, manufacturing processes have undergone a revolutionary transformation with the advent of 3D printers. These remarkable devices have brought about a paradigm shift in the way products are conceptualized, designed, and produced. With their unique capabilities, 3D printers have introduced a new era of efficiency, flexibility, and creativity to the manufacturing industry. This article delves into the significant impact of 3D printers on production efficiency, exploring the various ways they have transformed traditional manufacturing methods.
Introduction
3D printing, also known as additive manufacturing, has brought a revolutionary change to the manufacturing landscape. This technology allows the creation of three-dimensional objects by adding material layer by layer, contrasting with traditional subtractive methods. The positive impact of 3D printers on production efficiency is multifaceted and far-reaching.
The Evolution of 3D Printing Technology
Initially developed in the 1980s, 3D printing has evolved from producing basic prototypes to intricate, fully functional components. As the technology advanced, the range of printable materials expanded to include metals, polymers, ceramics, and even food. These innovations have broadened the scope of applications across industries.
Streamlining the Prototyping Phase with Rapid Iteration
Traditional prototyping was time-consuming and costly. With 3D printers, designers and engineers can quickly produce prototypes, iterate designs, and make necessary modifications without the need for extensive tooling changes. This accelerated iteration process significantly reduces development times.
Reducing Material Waste and Costs
Traditional manufacturing often generates substantial material waste. 3D printing produces minimal waste by using only the necessary amount of material. This not only saves costs but also contributes to a more sustainable approach to production.

Customization and Personalization at Scale
3D printing enables customization and personalization of products on a mass scale. Each item can be tailored to individual specifications without incurring additional costs or slowing down production. This level of customization was previously unattainable.
Complex Geometries Made Feasible
3D printing can fabricate complex geometries that are difficult or impossible to achieve using traditional methods. This opens up new design possibilities and allows engineers to create innovative structures that optimize performance.
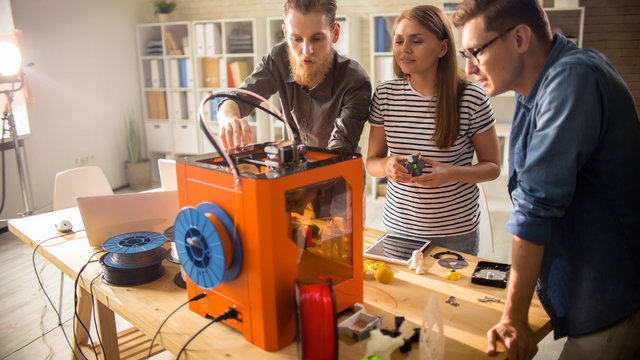
Shortening Supply Chains and Enhancing Logistics
By producing components locally using 3D printers, supply chains can be shortened, reducing lead times and transportation costs. This is particularly advantageous for industries requiring on-demand production and rapid delivery.
Empowering Small-Batch and On-Demand Production
Traditional manufacturing often favors large production runs to justify costs. 3D printing makes small-batch and on-demand production economically viable, enabling businesses to respond swiftly to market demands.
Enabling Rapid Tooling and Jig Production
3D printers can produce tooling and jigs at a fraction of the time and cost of traditional methods. This agility in tooling fabrication improves production processes and reduces downtime.
Accelerating Research and Development
The rapid prototyping capabilities of 3D printing expedite research and development efforts. Concepts can be quickly turned into physical models for testing and evaluation, expediting the innovation cycle.
Impact on Traditional Manufacturing Jobs
While 3D printing brings numerous benefits, concerns about job displacement arise. However, the technology also creates opportunities for new roles, such as 3D design, printer operation, and maintenance.
Sustainability and Eco-Friendly Production
The minimal waste produced by 3D printing aligns with sustainable manufacturing practices. Additionally, localized production reduces the carbon footprint associated with transportation.
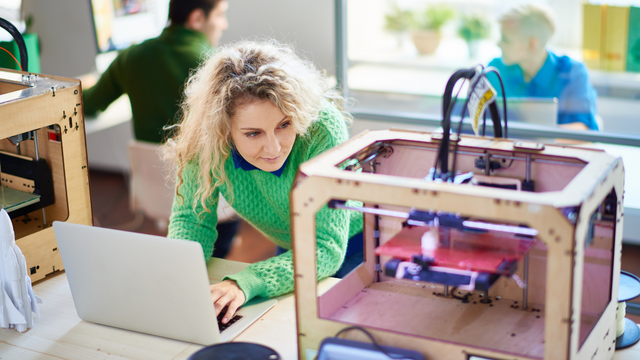
Quality Control and Consistency
3D printing’s digital nature allows for precise control and consistency in production. The digital file used for printing ensures uniformity across batches.
Challenges and Future Prospects
Challenges like material limitations, printing speed, and post-processing are being addressed through ongoing research. The future holds potential breakthroughs that could further enhance 3D printing’s capabilities.
Conclusion
3D printing has revolutionized manufacturing by enhancing production efficiency and opening new horizons of design and customization. Its positive impact spans across multiple industries, promising a future where traditional manufacturing methods are seamlessly integrated with innovative 3D printing technologies.
FAQs
What is 3D printing?
3D printing, also known as additive manufacturing, is a process of creating three-dimensional objects layer by layer using digital design files.
How does 3D printing improve production efficiency?
3D printing reduces lead times, minimizes material waste, allows for rapid iteration, and enables on-demand production, thus enhancing overall efficiency.
Can 3D printing replace traditional manufacturing?
While 3D printing offers unique advantages, it may not fully replace traditional manufacturing methods due to certain material and scale limitations.
What industries benefit the most from 3D printing?
Industries such as aerospace, healthcare, automotive, and consumer goods benefit significantly from 3D printing’s capabilities.